Tanner's Senior Project
R/C Baja
Construction
Summary:
The main construction method has been using the MakerBot 3D printer to manufacture components using ABS plastic. Additionally, some machining in the lab using the bandsaw, power drill and file to cut, shape, and drill holes to their appropriate dimensions. Lastly, the Bridgeport knee mill was used to drill holes for mounting components to the carbon fiber chassis.
Drawing Tree:

Figure 1: Drawing Tree
Part Construction:


Figure 1: Swing-Arm SR-30 Disolving
Figure 1 is an image of Team RC Baja's swing arms after being 3D printed. The swing arms were printed using SR-30 support material. This is the material in the white. The picture on the right is the ecoworks cleaning agent tabs dissolving the support material off of the swing arms to ensure the part has a smooth surface finish after being machined.
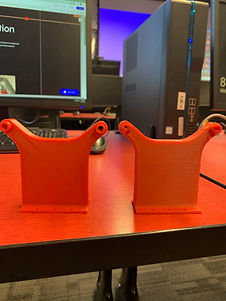
Figure 2. Front view shock tower

Figure 3. Right view shock tower

Figure 4. Supports in makerbot
Figures 2 and 3 are images depicting both attempts working on the front shock tower. For figures 2 and 3 the shock tower on the right was the shock tower when printed vertically without supports. The tower on the left hand side is the shock tower when printed on its backside using supports. Figure 4 is an image of the breakaway supports being used while 3D printing the rear shock tower on its backside using supports.

Figure 5: Extruder failure
Figure 5 is an image of one attempt of the rear shock tower. When printing the rear shock tower the raft unstuck itself from the bed. This caused the print to fail and the material to bulk up on the MakerBot's extruder.

Figure 6: Drilling to larger diameter
Figure 6 shows Tanner drilling out the holes connecting the steering knuckle to the lower control arms to a larger diameter.

This is a video of Tanner drilling out holes on the rear shock tower to the proper diameter. The holes cut on the carbon fiber chassis were larger than the holes 3D printed on the shock tower. To solve the problem holes were drilled on the suspension tower using the Bridgeport knee mill to the same diameter as the chassis.